From concept to reality: How can Chinese custom furniture accurately restore your design dream | Authoritative guide to avoid pitfalls
A detailed cross-border customization roadmap reveals how to make a Chinese factory thousands of miles away perfectly reproduce the furniture design in your mind.
When the design inspiration and the manufacturing factory are thousands of miles apart, the secret to accurate restoration lies in deep collaboration, transparent processes and scientific quality control.
Have you ever repeatedly pondered in the design software just to outline the perfect furniture outline in your mind? Every arc, every material combination, and every functional detail carries the infinite longing for the ideal space. However, when the design drawing is completed, finding a manufacturer who can accurately turn the drawing into reality becomes a huge challenge.
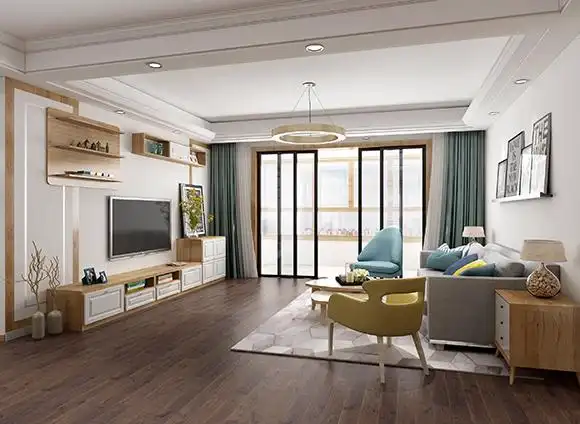
Standardized products in the local market are often misaligned with unique needs, and the size, color, and texture are always difficult to meet people’s expectations. At this time, China’s powerful custom furniture manufacturing industry has shown great appeal with its unparalleled flexibility, craftsmanship depth and cost advantages.
However, the journey of customizing high-quality furniture across the ocean is not a smooth journey. Can the design intention be accurately understood? Can the craftsmanship details be perfectly presented? Can the quality of the physical object match expectations? These doubts make many designers and buyers hesitate.
This article will analyze in depth how to systematically overcome the obstacles of remote customization and ensure that your design vision is intact from drawings to finished products, even if the manufacturing source is far away in China.
1. Accurate transformation of design intent: zero error from drawings to processes
- Core of the challenge: Complex design drawings are prone to misunderstandings during cross-cultural and cross-regional transmission.
- Solution: Establish a standardized and visual design communication system.
- 3D model confirmation: Require manufacturers to provide 3D renderings or animations of key nodes to intuitively display the structure, proportions and assembly logic. Research by the Industrial Designers Society of America (IDSA) shows that Visual communication can reduce manufacturing error rates by up to 40%.
- Detail annotation platform: Use online collaboration platforms such as TraceParts to annotate drawings, clearly indicating key dimensions, tolerance requirements, special processes (such as chamfers, splicing methods), and surface treatments (matte/bright, texture).
- Physical samples first: For key materials (wood veneer, fabric, stone texture, metal brushed effect) and special processes (carving, special paint, hardware texture), physical samples must be made for confirmation to ensure that the visual and tactile feel meet expectations. Large factories in major furniture industrial belts in China, such as Foshan and Dongguan, generally have the ability to quickly make samples.
Design drawings are blueprints, 3D models are common language, and physical samples are quality contracts. All three are indispensable.
2. Strict material selection system: The foundation of quality cannot be compromised
- Core of the challenge: Risks of inferior materials, unknown sources, and substandard environmental protection.
- Solution: Establish a transparent material traceability and certification system.
- Source certification: Suppliers are required to provide traceability documents for core materials, such as FSC certification (Forest Stewardship Council certification) for wood to ensure sustainable sources; LWG certification (Leather Working Group certification) for leather to focus on environmentally friendly tanning; CARB certification (California Air Resources Board certification) for panels or more stringent ENF grade standards to ensure formaldehyde release safety. Reference: FSC certification official website, LWG audit standards.
- Batch locking and inspection: Before mass production, the material batch is locked and the supplier is required to provide a third-party test report for the batch of materials (such as issued by SGS, ITS). The “Implementation Rules for National Supervision and Sampling of Furniture Product Quality in 2022” issued by the State Administration for Market Regulation of China has clear testing requirements for material safety performance.
- Key material sealing: Not only small samples, but also physical sealing of specific batches of materials (especially natural materials such as veneer and marble) to be used in mass production, signed and confirmed by both parties, as the “gold standard” for mass acceptance.
The soul of the material determines the life of the furniture. Authoritative certification is a pass, batch testing is a verification certificate, and physical sealing is the ultimate guarantee.
3. Concrete and digital monitoring of process standards
- Core of the challenge: The process standards are vague, rely on workers’ experience, and the quality fluctuates greatly.
- Solution: Transform the abstract “exquisite craftsmanship” into quantifiable and verifiable concrete standards.
- Operation instructions: Require suppliers to formulate illustrated operation instructions for key processes (such as mortise and tenon structure, special-shaped grinding, soft packing filling, and joint seam processing) to clarify the steps, tools, parameters and acceptance criteria.
- Process image recording: For key process nodes (such as frame assembly, initial grinding, before painting/spraying, and finished product assembly), high-definition photos or short videos are required to be taken and sent back for confirmation in real time. Alibaba International Station’s “Cross-border Customized Furniture Quality Control White Paper” points out that Process image monitoring can make the problem discovery node 70% earlier on average, significantly reducing rework costs.
- Introduction of intelligent detection: Factories with conditions are encouraged to use simple intelligent equipment to assist in key workstations (such as size detection and coating uniformity inspection) to improve accuracy and efficiency.
Craftsmanship is the skeleton and skin of design. Standard visualization makes requirements clear, process imaging makes progress transparent, and intelligent assistance makes accuracy controllable.
4. “Embedded” quality control throughout the entire process
- Challenge core: Unable to visit the site in person, post-inspection is risky and costly.
- Solution: Deeply embed quality control into the entire manufacturing chain, changing “post-blocking” to “process prevention”.
- Professional QC on-site or regular flight inspections: For core or high-value orders, entrust third-party professional quality inspection agency personnel to be on-site or conduct high-frequency, unannounced flight inspections. Globally renowned institutions such as SGS, BV, and Intertek have a complete service network in China’s manufacturing center.
- First-piece confirmation at key nodes: After mass production begins, the first-piece product must be fully disassembled and inspected (internal structure, materials, and process) and functionally tested. Production can only continue after confirmation.
- Segmented acceptance and process sampling: Production is divided into multiple stages (such as white body completion, painting completion, and assembly completion). At the end of each stage, sampling is carried out and a report is issued. AQL sampling standard (acceptable quality level) is adopted to scientifically quantify risks. Reference: Introduction to ISO 2859-1 AQL sampling standard.
- Ultimate destructive test: Randomly select samples from bulk goods for destructive testing (such as structural load-bearing, hinge life, and material composition analysis) to verify the limit performance and internal consistency.
Quality is manufactured, but also designed in and managed. Third-party embedding provides an objective perspective, segmented acceptance intercepts process risks, and destructive testing reveals the true bottom line.
5. Efficient and transparent collaboration and communication ecosystem
- Core challenges: Communication delays and misunderstandings caused by time differences, language, and cultural differences.
- Solutions: Build a structured, tool-based communication platform and specifications.
- Exclusive project collaboration platform: Use professional tools such as Trello, Asana, Basecamp or WeChat for Enterprise/DingTalk International Edition to centrally manage tasks, documents (drawings, standards, reports), time nodes, and communication records to ensure that information is never lost and responsibilities are clearly traceable.
- Fixed window period and escalation mechanism: Clarify the daily/weekly fixed online communication time window for both parties (such as afternoon in China corresponding to morning in Europe and the United States). Establish a clear problem escalation path (operator->engineer->project manager->management) to ensure timely decision-making on major issues.
- Bilingual technical coordinator: Ensure that there is at least one coordinator with bilingual skills and technical background in both teams, who is responsible for the accurate conversion of technical terms and the communication of intent to avoid ambiguity. MIT Supply Chain Management Project found that establishing a full-time coordinator can improve the efficiency of cross-border project communication by more than 35%.
- Regular progress visualization report: Suppliers need to regularly provide standardized reports containing pictures, videos, key data (completion percentage, problem points, and pending decision items).
Communication is the lifeblood of remote customization. The structured platform is the carrier, the professional coordinator is the bridge, and the visualization report is the signpost.
6. Risk pre-positioning control and worry-free delivery guarantee
- Core of the challenge: Hidden costs such as transportation damage, customs clearance delays, and no after-sales service.
- Solution: Systematically plan logistics, clarify responsibilities, and reserve plans.
- Professional packaging solution certification: Require suppliers to provide and actually test packaging solutions (especially for fragile parts, glass, mirrors, and sharp corners), and provide packaging test reports (such as ISTA transportation test standards). Reference: ISTA Transportation Test Overview.
- Full insurance coverage: Purchase cargo transportation insurance that covers the entire journey (from factory to final destination), and clearly define the starting and ending points of insurance liability and the claims process. Consider product liability insurance.
- Spare parts and quick response: The contract clearly requires suppliers to provide key vulnerable parts (such as specific hardware, glass panels, remote controls) or a complete set of spare parts. Establish a clear after-sales problem response process and time commitment (such as providing solutions within 48 hours).
- Localized cooperation resources: Establish a cooperative relationship with reliable local furniture installation and maintenance teams to solve the “last mile” installation and possible minor repairs.
Risk foresight is the work of the wise, and only with a complete plan can you rest assured. Professional packaging to resist road bumps, comprehensive insurance to transfer unexpected losses, spare parts and local support to ensure worry-free implementation.
When the lines on the design cross the ocean and obtain precise physical forms in Chinese factories, it is supported by a set of precisely operated collaborative systems. From the molecular structure of materials to the mechanical bite of mortise and tenon joints, from the optical reflection of paint to the cushioning coefficient of packaging, every detail can withstand scientific testing and standard measurement.
Made in China has long surpassed the single label of “cost advantage”. Its core value lies in integrating scattered manufacturing capabilities into a flexible network that responds to global personalized needs. When the designer knows how to control this system – anchoring the design intent through visual communication, locking the material gene with authoritative certification, relying on digital monitoring throughout the process, embedding the quality defense line with the help of professional quality inspection, building efficient collaboration to break through information barriers, predicting risks and improving delivery guarantees – thousands of miles away are no longer an obstacle.
よくあるご質問
Q1: How to ensure Chinese factories understand my design?
A: Use 3D models + physical samples + digital annotation tools for zero misinterpretation.
Q2: How to verify material quality remotely?
A: Demand FSC/LWG/CARB certifications + batch testing reports + physical sealed samples.
Q3: What’s the most effective remote quality control method?
A: Embedded third-party QC + stage inspections + destructive testing on random samples.
Q4: How to overcome communication barriers?
A: Use Trello/Asana + bilingual coordinator + fixed communication windows + visual reports.
Q5: How to prevent shipping damage?
A: ISTA-certified packaging + full insurance coverage + spare parts inclusion.
Q6: What if the final product has defects?
A: Contractual 48h response commitment + local repair partnerships + backup components.