Spring steel wire: the invisible backbone of sleep technology
Abstract: The core secret of a comfortable and durable mattress is often hidden in countless interwoven spring steel wires. The diameter, strength, toughness, surface quality and chemical composition of the steel wire, these seemingly cold parameters, together weave a sophisticated network that supports our sleep every night. This article will deeply analyze the five key dimensions of mattress spring steel wires, revealing how they determine the support, comfort and service life of the mattress, to help you make scientific choices and embrace a truly high-quality sleep experience.
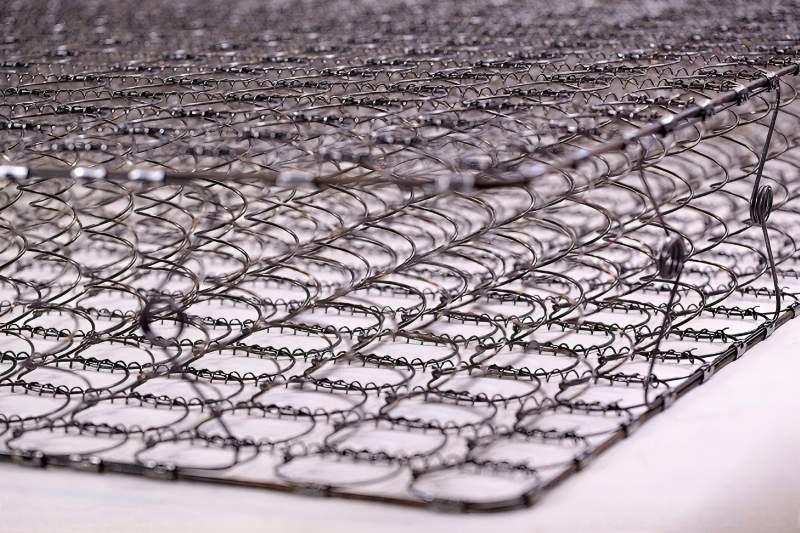
When we sink into a soft mattress for a night’s sleep, few people realize that what really supports this comfort and health are countless precision-designed and high-performance spring steel wires. They are the invisible skeleton of the mattress, and the difference in their parameters is enough to subvert the quality of sleep and the durability of the mattress for the whole night.
1. Diameter determines everything: the precise balance of support and comfort
- Argument: The diameter of the steel wire (1.8mm – 2.8mm) is the primary factor in determining the stiffness of the spring. Thick diameter wire (2.2mm – 2.8mm) is like a solid beam in a building, providing strong support. For those who are heavier (>100 kg) or prefer a hard mattress, it can effectively resist collapse and maintain the shape of the mattress for ten years (research by the International Sleep Products Association (ISPA)) continues to emphasize the importance of support for spinal health). Thin diameter wire (1.8mm – 2.2mm) shows excellent flexibility and fit, and can follow the body curves as delicately as flowing water, providing just the right cushioning for people who pursue a soft touch like clouds.
2. Strength builds the foundation: double guarantee of compression resistance and durability
- Argument: Strength is the core indicator of spring steel wire’s resistance to external force damage. Tensile strength (1800-2200 MPa) represents the ultimate ability of steel wire to resist breaking. Especially in the independent pocket spring system, when the human body rolls and generates complex tension, high tensile strength (such as ≥2000MPa steel wire used in high-quality products) is the key to the long-term service of the spring and avoid breaking. Yield strength (1500-1900 MPa) ensures that the spring only undergoes elastic deformation under pressure day after day – bending when under pressure and perfectly rebounding after the pressure is released. This is like the “memory point” of the spring, which is the core physical basis for the mattress to maintain elasticity and comfort for a long time (the standard test of the American Society for Testing and Materials (ASTM)](https://www.astm.org/) has strict regulations for this).
3. Toughness contains vitality: the source of vitality for extension and resistance to breakage
- Argument: Toughness index gives the spring “tolerance” and vitality when it is under stress. Elongation (≥8%) means that the steel wire can be significantly stretched and extended before breaking, avoiding brittle fracture like glass, which greatly improves the survivability of the spring in dealing with sudden overloads (such as heavy objects falling). The cross-sectional shrinkage rate (≥40%) reflects the plastic deformation ability of the material under extreme tension in a deeper level. The higher the value, the more uniform and dense the internal structure of the steel wire is, the better the toughness is, and it is less likely to cause internal damage and fatigue fracture under complex alternating stress (Related metallurgical research shows that high cross-sectional shrinkage rate is a key microscopic representation of material toughness).
4. Comprehensive surface protection: silent guard of rust prevention and wear reduction
- Argument: The surface of the steel wire is the first line of defense against environmental erosion. The thickness of the galvanized layer (10-20 microns) plays a key role in rust prevention. Especially in humid environments (such as southern China), a sufficiently thick galvanized layer can effectively isolate water vapor and oxygen, preventing the spread of rust from causing spring failure, mattress collapse and abnormal noise. Surface finish is also not to be underestimated. The smooth surface not only reduces the risk of cracks caused by surface defects (such as scratches and pits) when the steel wire is wound into springs at high speed, improves the production yield, but also ensures that the spring is in smooth contact with surrounding parts (such as frame connections), significantly reduces the “squeaking” noise caused by friction, and protects quiet sleep.
5. Elements give soul: the microscopic code of alloy synergy
- Argument: The performance code of steel wire is hidden in the precise ratio of its chemical composition. With iron (Fe) as the matrix, the synergistic effect of trace alloy elements is crucial:
- Carbon (C, 0.5%-0.8%): The core element for improving strength and hardness. The content needs to be delicately balanced – too low will lead to insufficient support, too high (>0.8%) will significantly damage toughness and increase the risk of brittleness.
- Silicon (Si), manganese (Mn): The “golden partner” for strengthening and toughening. They can refine grains, improve uniformity of organization, and comprehensively optimize strength and toughness (Journal of Materials Heat Treatment discusses the effects of Si and Mn on the microstructure and properties of steel wire in many papers).
- Chromium (Cr), vanadium (V): “enhancers” of durability. They significantly improve the corrosion resistance and fatigue resistance of steel wire. For mattress springs, which need to withstand millions of compression-rebound cycles, adding Cr and V can effectively delay the initiation and expansion of fatigue cracks, which is a microscopic guarantee for extending the service life of mattresses (often more than 10 years).
6. Collaborative Value Creation: The Ultimate Sublimation of Sleep Experience
- Argument: The above parameters do not exist in isolation, but work together on the final sleep experience. A mattress designed for large users needs to combine larger diameter (for firm support), high strength and high toughness (for durability), thick galvanized layer (for rust protection) and Cr/V alloy formula (for fatigue resistance); while a mattress designed for those who pursue ultimate comfort needs to focus on smaller diameter (for delicate fit) and optimized toughness (for smooth response), while surface finish (quiet) and corrosion resistance (for long-lasting like new) are still the basic guarantees. Understanding the synergy of these parameters is the scientific cornerstone for manufacturers to design excellent products and consumers to make wise choices.
Резюме:
Mattress spring wire, this seemingly ordinary metal wire, is actually the exquisite crystallization of science and engineering in the field of sleep. From the diameter that determines the support stiffness to the strength and toughness that ensures the long-lasting structure; from the surface protection that protects health to the alloy code that gives excellent performance – each parameter profoundly affects the quality of our rest every night and the service life of the mattress. When choosing a mattress, looking beyond the surface comfort and paying attention to its inner “wire spine” is a wise investment in your own healthy sleep. Let scientific parameters guide your choice and let the precision springs carry you for a deep sleep every night.